工程塑料 |
|
| 按行业筛选 |
|
|
| 按产品筛选 |
|
|
| |
查看本类全部文章 |
| |
|
|
|
无机粉体填充塑料的轻量化技术进展 |
|
作者:刘英俊 陈凌 |
|
碳酸钙(包括重钙、轻钙)、滑石粉、重晶石粉、高岭土等无机粉体材料在塑料中的应用已十分广泛,年用量多达1000余万吨。众所周知,这些粉体材料在国家经济建设和人们社会生活中发挥着重要作用,一是节省了大量以石油为基础原料的合成树脂;二是改善了塑料材料某些方面的性能,如韧性、刚性、耐热性等;三是赋予了纯基体塑料不可能有的功能,如阻燃、抗静电、耐候等。更为明显的是无机粉体材料与合成树脂之间的差价巨大,填充塑料材料的原材料成本将明显低于单纯的塑料材料,而性能价格比的大小是企业及产品市场竞争力高低的最重要因素。改革开放三十多年来,填充改性塑料行业的蓬勃兴起和发展,在塑料中尽可能多地使用无机粉体材料无疑已成为不可阻挡的潮流。
当无机粉体材料填充改性塑料发展到一定阶段时,使用无机粉体材料的一些负面影响也清晰地显现出来,其中最主要的影响就是“增重”现象,即填充塑料材料的密度显著增大。如纯聚丙烯塑料的密度为0.91g/cm3,纯聚乙烯塑料的密度依低密度、线性低密度和高密度三种不同类型,其密度从0.92g/cm3至0.96g/cm3不等,而当聚乙烯或聚丙烯基体塑料中加入碳酸钙后,其填充体系的密度会显著增大,这种“增重”现象在注塑成型塑料制品或模压成型塑料制品中最为突出,例如含有15%重质碳酸钙的聚乙烯注塑制品其材料的密度达到1.1g/cm3以上,含有30%重钙的聚乙烯注塑制品其材料的密度达到1.3g/cm3左右,80%含量的重钙填充母料,注塑成型试片的密度约1.8g/cm3,如果用模压法制成的试片,其密度甚至会达到2.0g/cm3。
由于注塑成型塑料制品是按制件个数计价,挤出成型塑料制品(如管材、型材、膜片等)是按长度或面积计价,如果使用无机粉体材料带来的原材料成本降低而产生的效益,抵不过因密度增大使制品个数减少或长度、面积缩水产生的损失,塑料制品加工企业就会丧失使用无机粉体材料的积极性,更不用说填充塑料材料某些方面的性能因无机粉体材料的存在而有所降低了。
发泡是填充塑料降低密度实现减重轻量化的重要途径
发泡——使塑料材料呈现多孔结构是降低塑料材料密度的重要途径。可发性聚苯乙烯经发泡工艺成型后,其材料密度可降低到0.03g/cm3,聚氯乙烯发泡板的密度也可以达到0.7g/cm3左右。但一方面这些发泡材料的力学性能已经大大降低,另一方面不可能适应一般塑料制品的成型加工工艺,而且最重要的问题,无论是物理发泡机理,还是化学发泡机理,由于聚乙烯或聚丙烯的熔体强度低,其熔体分子形成不了有效的泡孔壁,造成气体逃逸,泡孔塌陷,无法形成结构规整的发泡材料。加入无机粉体材料后,问题更为复杂。上世纪90年代中期,有的企业曾试图在PE箱包片材、帽舌芯层等产品中加入发泡剂,制成一定发泡倍率的材料,结果出现刚性不足、板面软化、无回弹性、针孔掉线、易变形等多种问题,如果使用填料以提高片材的刚性,仅仅加入5%的填料,就出现密度上升、产品厚薄不均、爆板、流痕等问题。
无机粉体材料填充聚乙烯材料及制品的成功例子是上世纪八十年代曾经流行一时的钙塑天花板以及一直延续到现在的聚乙烯微发泡拖鞋、凉鞋制品,但这些产品的制造工艺无一例外地使用了交联剂,即在发泡剂分解产生气体并形成致密的微孔结构时,是交联剂把聚乙烯熔体的分子凝结成有效的气孔壁,包裹住了气体。这种经过交联的聚乙烯材料其柔性十足,但强度和刚性不足,对绝大多数聚乙烯制品来说是不适合的,而且更为关键的是经过交联的塑料材料,已形成体型分子,很难再回收利用,其生产过程中产生的边角料也无法及时回收做为原料使用。从当前绿色生态的角度看,依靠交联形成有效的泡孔结构是走不通的。
聚丙烯塑料具有非常良好的物理机械性能,其耐热性能突出更是五大通用塑料中最优的,通常可以在100℃环境下长时间工作,在无负载的情况下其工作温度甚至可以达到130℃。但聚丙烯是半结晶性聚合物,在达到170℃左右后,其结晶区迅速解体,一旦熔融其熔体粘度迅速下降,无法包裹住发泡剂分解产生的气体形成有规则的泡孔结构。多年来针对这一关键难点进行研究,其解决途径是制造高熔体强度聚丙烯(HMSPP)。
HMSPP由于熔体强度高,有利于形成均匀致密的泡孔,但因在制备过程中面临聚丙烯降解和凝胶两大问题以及聚合物接枝反应与单体均聚反应的竞争、聚合物主链断链和交联与支化的竞争,不仅生产技术复杂、难以控制,而且加工成本增大使产品的售价较普通聚丙烯高出40%以上,成为不能大规模推广应用的主要原因。
多年来,不使用交联工艺,也不使用高熔体强度聚丙烯的无交联发泡聚烯烃加工技术的研究一直在进行之中,特别是在有大量无机粉体材料存在的情况,能够实现普通聚乙烯或聚丙烯发泡是目前国内外最为关注的技术领域。我们利用无机粉体自身的特性,并对其进行必要的表面处理后,使其不仅扮演填料的角色,还可有助于发泡材料形成泡孔结构,其发泡材料的刚性、稳定性、硬度、弹性模量等力学性能也同时得到保障,满足塑料制品的使用要求,从而达到降低填充塑料密度,真正实现降低成本、提高性能价格比,增强产品市场竞争力的目的。
非交联发泡减重技术在PP发泡片材上的应用
1)含有20%重钙的PP发泡片材的物理力学性能见表1。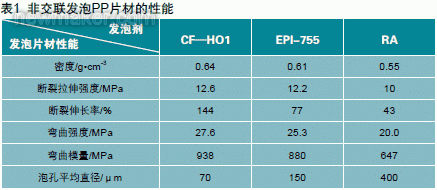 2)技术关键
● 重钙粉体的选择
重钙粉体不仅起到填充作用,而且要在成型过程中起到成核剂的作用,粒径过大或过小,都不利于良好分散的同时又具成核功能。通过研究和生产实践,6.5μm左右的重钙粉体最为适用。
● 重钙粉体表面处理
首先要对粉体预热和除湿,严格控制水份,然后在一定温度下依次加入偶联剂、多元醇表面活性剂等助剂。
● 用高速混合机混合时要使原辅材料得到充分混合,同时又要严控物料温度,当前还要采用负压真空式上料以减轻粉尘外扬现象。
● 发泡填充母料中的造粒工艺既要保证物料良好塑化,又要保证不破坏物料中的发泡体系,使发泡剂在造粒过程中不损失。实际生产时采用双阶混炼挤出加工设备。
轻质聚乙烯薄膜复合母料(发泡填充母料)
由上海润龙包装用品有限公司研究开发、辽宁金科塑胶科技有限公司生产的,荣获发明专利授权(专利号:ZL200710173739.2)的轻质聚乙烯薄膜复合母料(发泡填充母料)可有效克服塑料制品在添加非矿粉体时产生的密度增大和力学性能下降过大的问题。
使用传统填充母料和该专利母料时,塑料薄膜的性能见表2。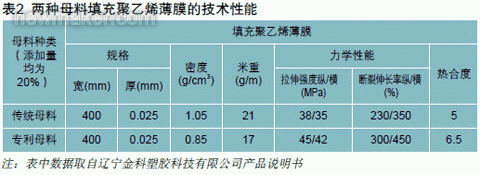 采用高孔隙率粉体做填料降低填充塑料的密度
1)以往的做法及面临的问题
粉体颗粒如果呈现多孔状,堆积在一起体积就比较大,即堆积密度小。就像轻钙和重钙因晶形不同的堆积的紧密情况有所差别,从而二者的堆积密度有显著差别,沉降体积就有所不同。尽管在添加到塑料中后,多孔性的粉体一些孔隙被高分子树脂或助剂占据,但仍然保存着众多孔隙,就如同发泡塑料一样,材料中夹杂着一定量的空气,从而使填充塑料的密度较之加入同样份数实体粉体材料,其密度显著降低。
天然非金属矿物中,硅藻土和沸石是典型的高孔隙率的多孔隙粉体,在过去的生产实践中也确实证实了其高孔隙率可以降低填充塑料的密度。但下述问题妨碍了这两种粉体的普遍应用。
A. 硅藻土和沸石的硬度远远大于重钙、轻钙等各种常用填料,易对接触的加工设备及模具造成严重磨耗。
B. 硅藻土和沸石的表面处理困难,影响与基体塑料的亲合性,从而使填充塑料的力学性能严重劣化。
C. 天然矿物资源有限且不可再生。
2)人工合成硅酸钙的应用在实现填充塑料轻量化道路上展现光明前景
以硅(Si)元素为关注对象的人工合成硅酸钙粉体呈现多孔特征,具有高孔隙率,见图1,其它四种粉体的颗粒形状见图2。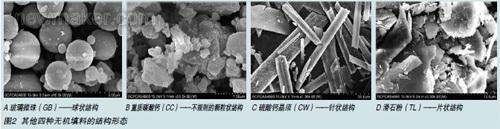 由图1 可见, 合成硅酸钙微粉颗粒是一次性颗粒聚集成的二次或三次颗粒团聚体, 一次颗粒粒径1~3μm, 二次或三次颗粒的粒径为10~30μm。硅酸钙微粉颗粒的内部具有丰富的微孔结构,呈蜂窝状,其微孔尺寸约100nm,微孔周边孔壁厚度5~10nm。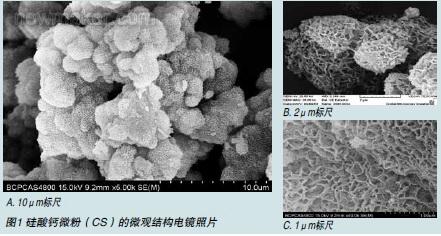 表3和表4分别展示了硅酸钙微粉和其它多种粉体的物理性能。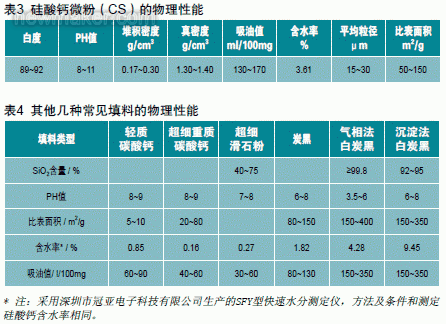 和其它常用的粉体相比,硅酸钙微粉具有堆积密度和真密度小、吸油值高、含水多、比表面积大等显著特点。
通过不同粉体填充聚乙烯塑料的试验可知,在不同添加量时,五种粉体对填充聚乙烯塑料密度的影响如图3。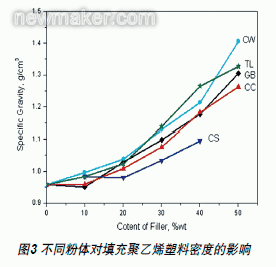 由图3可见,同样添加量时,硅酸钙微粉(CS)填充的聚乙烯塑料的密度明显低于其它粉体填充的聚乙烯塑料,而且随着添加量的增大,CS填充的聚乙烯塑料密度增大的十分缓慢,添加量达40%时,其填充塑料的密度不到1.1g/cm3,而其它粉体填充的聚乙烯塑料已高达1.15g/cm3以上了。
在同样添加量情况下,硅酸钙微粉填充的聚乙烯塑料的物理力学性能也有良好表现。
3)硅酸钙微粉在塑料制品生产上的实际使用效果
先将硅酸钙微粉制成填充母料,再在聚乙烯片材生产中按母料 : 聚乙烯树脂=40:60比例进行挤出加工,片材产品宽度为1.8m。将该片材与添加40%碳酸钙母粒的片材进行性能比较,其结果见表5。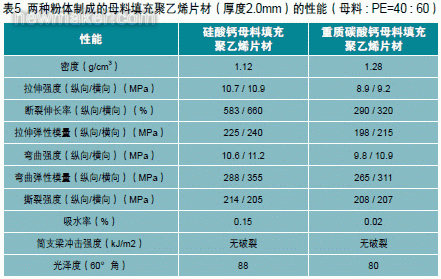 从表5可知,同样条件下,硅酸钙微粉的填充效果优于重质碳酸钙,其密度降低了10%以上。
对碳酸钙行业的希望
碳酸钙在塑料中广泛应用的重要意义不言而喻,但是增重问题是碳酸钙在塑料行业中继续扩大应用的瓶颈。实现填充塑料轻量化具有重要的现实意义和长远的战略意义,其经济效益和社会效益都十分显著。
硅酸钙微粉的出现为碳酸钙行业带来新的思路,因为硅酸钙微粉的生产过程大体和碳酸钙相似,其中钙元素的由来都是石灰(氧化钙),在最后形成硅酸钙的时刻,是氧化钙与体系中的硅化合物反应而成的。碳酸钙行业的专家和企业家们能否在重新反应成碳酸钙时使其成为多孔性的颗粒呢?希望总是可以有的,实现碳酸钙填充塑料的轻量化是我们共同的奋斗目标。
|
|
文章内容仅供参考
(投稿)
(如果您是本文作者,请点击此处)
(1/8/2015) |
对 工程塑料 有何见解?请到 工程塑料论坛 畅所欲言吧!
|