真空设备/泵 |
|
| 按行业筛选 |
|
|
| 按产品筛选 |
|
|
| |
查看本类全部文章 |
| |
|
|
|
离心泵技术在油气精炼中的应用 |
|
newmaker |
|
下游油气产业已经发展了约100年。炼油和天然气加工行业起源于20世纪初的美国,如今该行业规模庞大,技术成熟。
旋转机械技术在下游产业中起着重要作用。事实上,设备的工艺条件可能是很严苛的:一个正常大小的上游顶端设备的输出率可达1500吨/小时,还有一些关键的工艺节点,如炉内装料泵的温度接近800℃,这些加工过程都需要特殊的技术解决方案。流体催化裂化(FCC)设备要求进料首先与催化剂混合,然后泵送到温度达500℃左右的反应器里。这一过程所需的空气通常由正常流速约50000标准立方米/小时的离心式或轴流式压缩机来提供,功率可达数兆瓦。压缩和泵送应用场合中所采用的旋转机械对于保障加工过程的整体稳健性起着至关重要的作用,而在这些设备里,离心泵又是重中之重,它几乎参与了所有的工艺过程。
各种尺寸大小的离心泵遍布下游工艺应用。针对不同的应用,已经开发出许多种离心泵配置形式,从单一泵到多级泵,轴向或径向剖分式,卧式或立式转子。
图一:特定效率下的转速。 迄今为止,最常见的形式是卧式泵,它们适用的压力和温度范围广泛,工作压力可高达400巴,温度可高达450℃,而立式泵的应用范围比较有限,主要用在低汽蚀余量的工况和非常低的温度环境下。
许多大型制造商都为离心泵行业的发展做出了贡献。
技术法规和行业标准
对于流程工业泵,(美国石油协会)API 610标准和水力协会准则提供了一系列广泛而全面的指导方针,从而推动整个泵生产工艺的发展。这些标准由泵制造商和客户组成的董事会来制定,涵盖了从早期设计到车间制造阶段的主要方面。API 610标准已经及时得到了修正:用来评估泵效率的标准从以前的效率公差变成了针对整体吸收能力的实际公差。振动极限也做了类似的调整,反映了客户和制造商群体日益关注的问题,即延长泵的使用寿命和提高能效。
工厂管理层不断寻找最终的市场竞争力,促使离心泵技术在两方面得到了发展,一是提高性能,二是降低整体成本。下面的段落将简要介绍其中的一些技术改进。
金属材料技术的发展很重要。众所周知,在工作期间,泵会遭受侵蚀和腐蚀,产生疲劳现象。从设计的角度看来,要获得令人满意的机械使用寿命,首先必须确保选用合适的制造材料。材料技术的发展始于20世纪50年代,如今已经出现了许多能抵御上述现象的优秀材料。实际冶金过程对材料的化学特性具有较高的控制作用,例如双相钢(CD4MCU)或沉淀硬化17-4-PH特种钢常用于制造泵的轴。还有一些其他的例子,比如等离子或激光涂层这类创新工艺可以对套筒表面进行硬化处理,有助于提高耐磨性。计算机有限元分析方法的发展帮助我们更好地了解各个泵部件内部的应力场情况。
泵技术不断朝着性能更佳和运转速度更高的方向发展,因而极大地推动了泵转子动力学这一研究领域的发展。此外,还有一个重要因素,即计算技术的发展为业界提供了足够强大的计算能力。
现代旋转机械设计充分利用了经验优势和专用软件工具,有助于针对某些机械设计方面的问题进行细致的评估,如选择轴承,平衡活塞,确定轴套间隙的大小。所有这些因素以及边界设计操作条件结合在一起确保了转子的最终稳定性。
汽蚀
汽蚀是另一个众人皆知的影响离心泵的问题。它是由于流体汽化所造成的,在流体汽化过程中净压力会低于蒸气压力。下游压力的恢复使得蒸汽气泡突然内爆,导致叶轮表明出现凹点。汽蚀可能带来巨大的影响,使泵的性能逐渐降低,直到彻底失效。
图二:叶轮等压线速度矢量图 过去,专业的泵操作人员常常通过辨别具有特点的碎石噪音来检测汽蚀。振动研究的最新进展表明还能利用谐波(FFT)技术来检测发生的汽蚀现象,这样就能实现自动诊断。解决此问题的传统方法是在必须汽蚀余量(来源原始设备制造商)的基础上留有一定的静态安全裕度。一种有效的汽蚀监控方法是测量最靠近泵吸入点处的压力、温度和流速。
然而,以往永久安装的监控系统所用的次数非常有限,这样就显得监测系统的成本过高,特别是对于小型泵来说。市场上出现的经济实惠的逻辑控制器已经改变了这一状况,如今即使是小型的离心泵也能从这种控制和监测系统中受益。
另一项一直对泵技术改进做出贡献的因素是测试方法的研发。先进振动测量系统的商业可用性使得我们能够采集大量的数据。
接近探针和机体速度传感器使测试工程师能够对机械振动行为进行详细的检查,并找到机械参数、流量读数、性能、FFT频谱谐波分量和轨道形状以及一些特殊的干扰现象(如汽蚀或内流旋转失速等)之间的相关性。
计算流体力学的引入也影响了流程泵行业的发展。泵流型三维形状的水力设计实际上是一项棘手的任务。随着计算能力的逐步增强,以及可以利用可靠的设计程序,离心泵的设计过程得以持续完善改进,同时,还能将OEM经验和可靠的仿真预测结合起来。现代CFD(计算流体动力学)商用程序拥有先进的功能,可以对粘性和无粘性流体建模,提供多种湍流方程以及针对涡轮机旋转区域的非平稳算法。整个设计回路需要条条路线都闭合,并且通过OEM生产车间的最终机器物理测试,但是如果采用CFD方法就能在较短周转时间内实现更好的设计方案。计算机仿真有利于我们在较短时间内根据客户规定的工作条件,针对具体的优化目标(F.E.最大效率,汽蚀余量)研发出水力通道形状。当我们考虑是否能通过集成现代CAD/CAM技术来制造CFD设计出的定制液压零件时,这些科技上的进步就显得尤为重要。
控制系统的改进
如上文所述,离心泵广泛应用于石油和天然气行业。欧盟的相关数据显示能耗的绝大部分来自泵驱动器应用:中低功率范围总计几乎达到已安装的驱动器功率的总和,消耗了总能量的76%。
图三:等压线和流线 尽管这方面相当重要,但在过去十年,与目前使用非常先进的控制系统的大型泵相比而言,人们较少关注低功率泵的控制系统。这主要是因为小型泵的收益成本之比较低,而控制系统对于整个泵站成本有着很大的影响。表一:市场调研和分析结果
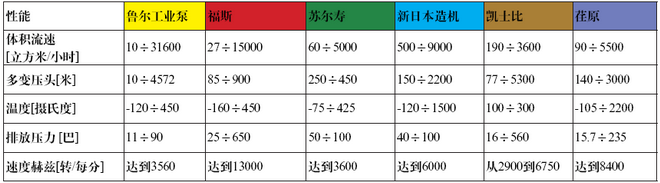 过去的一种冗余做法是安装多个备用件。这种冗余的方法对于多台泵的初始安装成本要求很高,并且在很多时候,如果泵一直工作直到报废,那么就显著增加了工作阶段的成本。相关的经济方面的负面影响不会出现在设备的初始设计阶段,而是出现在工作阶段。
如今安装专用的控制系统非常方便,即使对于低功耗/小型泵也是如此:集成VFD系统能节省大量能源,先进的自动诊断控制系统也有利于显著减少工作和维护成本(延长正常运行时间和最终的机器寿命)。表二:市场调研和分析报告结果
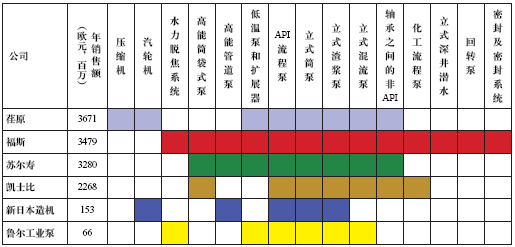 现代泵控制系统,如IPC PROTEO,利用工作现场已安装的最少数量的传感器实现了一个全面的泵自动化控制流程。如今得益于商用PLC系统计算能力的大幅提高,我们可以通过实施绩效模型(PBM)来实现这一目标。这些系统不仅能够执行机械控制任务,而且还可以对泵进行保护和自动诊断。与未受监控的安装情况相比,稍高的安装成本会被降低的维护成本,维修成本和生产停机时间所抵消。
图四:电机和相关的功耗 这类系统的主要特点和优势如下:
● 多变量控制功能:用户设置被控制的流程参数;系统对所有相关流程参数进行连续监测,并自动对需要保护机制干预的变量实施控制。
● VFD驱动器:与传统节流方法相比,这种驱动器能大幅降低功率吸收,从而达到更高的能效(甚至提高40%,这取决于具体的条件)。
● 可以利用机械模型的基于性能模型(PBM)来预测实际工作条件下的预期性能。现场测量技术使我们得以确定实际的性能。预期性能与实际性能的偏差即可使系统提供自动诊断指征(特别是一些异常现象,如汽蚀扰动,机械性能退化,变送器故障)并激活相关防护措施。
发展
本文讨论的泵技术的许多发展趋势正在不断发展。经验丰富的用户和泵制造商在涉及国际标准的重要工作领域相互交流。泵技术的长足进步为业界带来许多好处。正如前文所述,CFD是非常有趣的一个发展领域。目前还在研发如何在工控机(IPC)中将CFD和CAD/CAM集成,以利于实现创新的高效泵设计。实际上,通过综合应用这些方法,将有可能实现为每个具体的泵实例提供最优化的定制设计方案。
图五:PROTEO架构 与传统的根据产品一览表来挑选泵的方法不同,这种定制设计过程不仅能达到最高的设计效率,而且能获得上述讨论的所有好处。基于性能模型(PMB)的新控制系统和自动诊断软件算法(例如PROTEO)一旦与液压领域的这些先进技术相结合,那么将有望获得本文提及的其他好处。VFD驱动器能更好地管理工作时功率,将它与基于性能模型的控制系统集成在一起,就能实现节能,减少维护费用,并使正常运行时间最大化。新一代离心泵成功工作的关键因素就在于综合应用本文论述的所有这些方法。(end)
|
|
文章内容仅供参考
(投稿)
(如果您是本文作者,请点击此处)
(1/14/2016) |
对 真空设备/泵 有何见解?请到 真空设备/泵论坛 畅所欲言吧!
|