发动机 |
|
| 按行业筛选 |
|
|
| 按产品筛选 |
|
|
| |
查看本类全部文章 |
| |
|
|
|
缸盖生产线OP60座圈换型新方法的研究 |
|
newmaker |
|
近几年来,随着发动机技术的发展和客户需求的多样化,南汽工厂中的SE 缸盖生产线产品型号不断增多,在生产过程中产品换型的次数也明显增加,如何提高缸盖生产线的产品换型效率成为众多行业人士关注的问题之一,本文就此作了详细介绍。
换型背景
1、 缸盖功能:缸盖是发动机主要零件之一,它的作用是用来封闭汽缸上部,构成燃烧室,并为凸轮轴和进、排气歧管提供支撑。发动机工作时,空气从进气歧管吸进燃烧室,火花塞把可燃混合气体点燃,带动活塞做功,并把废气从排气歧管排出。
2、生产线:缸盖生产线共有34 台加工设备,19 道加工工序(见图1)。该条生产线是目前国内比较先进的生产线,加工精度高、生产效率快。工艺规划的产能为25 万台/ 年。涉及本次课题的工序是OP60,采用的是德国ELWEMA专机,工序名称为“压装气门座圈和气门导管”。
图1、缸盖加工工艺流程 3、ELWEMA 专机:采用常温方式对座圈和导管进压装(座圈和座圈底孔的过盈量为0.06-0.098mm,导管和导管底孔的过盈量为0.025-0.075mm)。座圈和导管的压装头均同时装有压力传感器和位移传感器,操作工可以通过压力- 位移监控系统对座圈和导管的压装状况进行实时监控,当出现漏压、压装不到位、压废(工件尺寸超差、压装件在压头上定位不准)、压斜等故障时,系统能够及时报警,防止不合格件流到下道工序中去。机械手从输送滚道上抓取工件到压装位置进行离线压装。
图2、ELWEMA 专用压装机 它的优点在于:输送速度快、压装位置(包括角度) 可以通过程序调整,也能满足产品换型的需要。在座圈压入过程中,有顶杆顶住气门弹簧底座位置,用于抵消压入力,防止工件变形。以下是压装前、后的缸盖局部三维视图(见图3 和图4):
图3、压装前状态
图4、压装后状态 4、座圈送料装置介绍:从气门座圈的进料到出料的过程来划分,该装置主要由4 段组成(见图5): ① 料斗内的升降器将座圈输送到检测装置;②分料器将筛选合格的座圈放行到料道入口;③气缸将料道入口处的座圈逐一打入料道中;④座圈最终被输送到料道的最末端(我们也称为“压装区”)。
图5、气门座圈送料装置 现状调查
1、工序换型时间统计:自1.5T 缸盖量产以来,OP60 的产品换型时间(1.5T ←→ 1.5VCT)达53 分钟,远远高于其它工序的产品换型时间(10-20 分钟),成为缸盖生产线产品换型的瓶颈工序,严重不符合精益生产的要求。
2、OP60 产品换型内容:1.5VCT 缸盖和1.5T 缸盖在OP60 的差异件是进气座圈和缸盖毛坯(见表1)。缸盖毛坯的差异可以通过OP50 二维码扫描装置来识别和防错;而进气座圈的差异只能通过目测来识别、通过隔离来防错。所以OP60 的产品换型指的就是座圈换型。表1、两种缸盖在OP60 的差异点统计
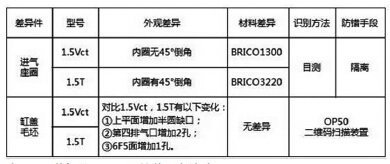 3、OP60 产品换型流程:过去,我们在OP60 一直采用的是集中换型法,主要是通过集中清空旧状态座圈、集中填补新状态座圈的方式进行座圈换型,集中换型法共有五个步骤,总用时为53 分钟(见表2),我们从价值流的角度来分析: 这些步骤不产生任何产品价值,由此产生的时间均是非增值时间。表2、集中换型法的步骤和时间统计
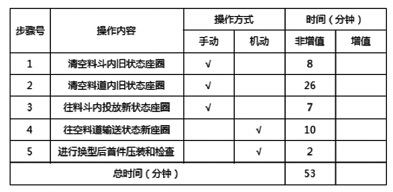 解决方案
在部门大力推行的“精益生产、降本增效”的要求下,鉴于缸盖生产线的产品换型时间最长,而OP60 又是缸盖生产线产品换型的瓶颈工序,所以,提升OP60 的换型效率刻不容缓。
1、提出方案。如何提升缸盖OP60 座圈换型效率呢?我们发挥头脑风暴,共提出了3 个解决方案,它们分别是:增加座圈上料机构、统一座圈型号、递进式换型。
2、方案选择。我们对方案一( 增加座圈上料机构 ) 的特点进行了分析,具体意见归纳如下(见表3):表3、方案一的特点分析表
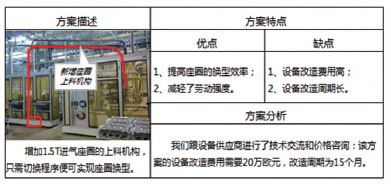 我们对方案二(统一座圈型号)的特点进行了分析,具体意见归纳如下(见表4):表4 、方案二的特点分析表
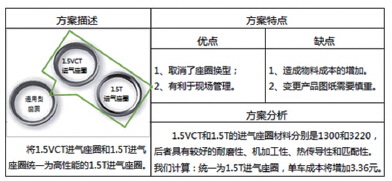 我们对方案三(递进式换型)的特点进行了分析,具体意见归纳如下(见表5):表5 、方案三的特点分析表
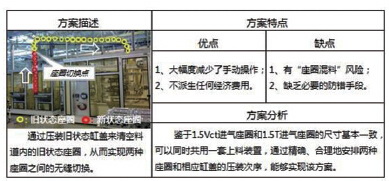 针对性的个案分析后,我们又从可实施性、经济性、时间性、有效性等方面对上述三个方案进行了系统评估和全面比较, 最终将递进式换型选定为最佳方案。
3、制定对策。找出要点:我们根据递进式换型的特点初步拟定了的相应的操作流程,为确保产品换型的成功,我们针对步骤一和步骤六提出了“旧状态的缸盖和座圈在数量上匹配”的要求;针对步骤二、步骤三和步骤六提出了“压装后被标识的座圈处于料道最末端”的要求。为满足这两个要求, 我们罗列了四个亟待解决的问题要点(见图6):①确认料道的座圈数量 ;②确认备用缸盖的数量 ;③确认备用缸盖的隔离方式;④确认标识座圈的方法,并以此作为制定对策的依据。图6、流程分析图图
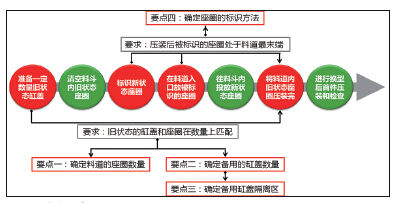 制定对策:我们根据上述要点制定了对策表(见表6),并明确了具体的对策、目标、措施、责任人、实施地点和时间节点。表6、对策表
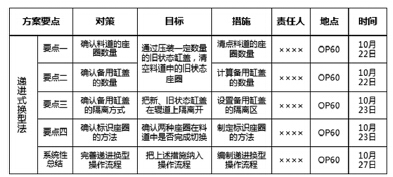 对策实施一:我们把一个已标识的进气座圈放入料道入口,启动设备后,我们便开始对从料道出口输出的座圈进行逐一计数,当被标识的座圈出现出现在料道出口时,计数结束, 这时的计数结果为224。也就意味着:料道的座圈容纳数应为224。
对策实施二:1 台四缸的NSE 缸盖有8 个进气座圈;料道的座圈容纳数量为224。我们通过计算得出:与料道内的座圈匹配的缸盖数量为28( 计算公式:224÷8=28)。也是就是说:我们可以用28 台旧状态缸盖来排空料道内的旧状态座圈。
对策实施三:我们利用OP40 的挡料装置和OP50 的二维码扫描装置,在它们之间的输送辊道上设置了OP60 产品换型隔离区(见图7 的红色区域),该区域可容纳28 台旧状态缸盖。OP40 的挡料装置就是新、旧状态缸盖的隔离点。
对策实施四:我们用记号笔在座圈外倒角一侧的端面上做上标记,座圈在料道内输送时该标记朝外(见图8)。这样,在压装一定数量的旧状态缸盖后,我们在料道出口处可以通过座圈上的标记目视确认两种型号的座圈是否完成了全面切换。
对策实施五:我们把上述措施的实施结果纳入递进式换型的操作流程,共有七个步骤:①在隔离区备28 台旧状态缸盖;②清空料斗内的旧状态座圈;③连续标识8 个新状态座圈; ④将标识的座圈放到料道入口;⑤往料斗内投放新状态座圈; ⑥把料道内旧状态座圈压装完毕;⑦进行换型后的首件压装和检查。
效果检查
图7、备用缸盖隔离区 1、换型方法的现场验证:2014 年11 月7 日我们按照上述操作流程在OP60 进行了一次从1.5VCT 到1.5T 的产品换型,总用时22 分钟。由于我们在步骤六中完成了28 台旧状态缸盖的座圈和导管的压装,实际产生了价值,所以该步骤的用时为增值时间,不计入换型总用时。
2、新旧换型法的对比:换型时间是如何节省下来的呢?我们通过两种座圈换型法的步骤和用时对比图(见图9)得出结论: 在三个步骤的内容相同情况下,递进式换型用4 个步骤取代了集中式换型的2 个步骤,导致座圈换型的总时间减少了31 分钟。
图8、标识座圈 计算公式:26(旧步骤二)+10(旧步骤四)-2(新步骤一)-2 (新步骤三)-1(新步骤四)=31(分钟)
3、换型时间的月度统计:2014 年11 月我们在OP60 共进行了8 次座圈换型,并把递进式换型法全面推广到1.5Vct、1.3 Base、1.5T、1.5Plus、1.5Plus(TT)、1.5T(TT)等产品型号上, 根据当月的现场统计:它们彼此之间的换型时间均不超过22 分钟,并且未发生一起“座圈混料”的质量问题。
4、换型时间的季度统计:我们以三个月的平均值计算, OP60 的座圈换型时间由优化前(2014 年8 月-11 月)的53 分钟降低至优化后(2014 年11 月-2015 年1 月)的22 分钟,达到了我们的改善目的,缸盖生产线各道工序的产品换型时间趋于一致,满足了线平衡的要求。
图9、两种座圈换型法的对比图 结束语
通过对缸盖生产线OP60 的座圈换型方法的研究,缩短了当道工序的产品换型时间、提升了缸盖生产线的生产效率、激发了员工在工作中的创新改善意识,形成了“人人都是管理者” 的活动氛围,也使员工在活动中受益匪浅。(end)
|
|
文章内容仅供参考
(投稿)
(如果您是本文作者,请点击此处)
(6/1/2015) |
对 发动机 有何见解?请到 发动机论坛 畅所欲言吧!
|