镗床/钻床 |
|
| 按行业筛选 |
|
|
| 按产品筛选 |
|
|
| |
查看本类全部文章 |
| |
|
|
|
自动化产品在机械加工机床中的应用 |
|
newmaker |
|
摘要:镗床是重要的机械加工机床之一,在该镗床控制系统中,采用贝加莱的PLC和伺服驱动装置实现对曲轴连杆镗床的精确控制,利用最小二乘法实现镗杆的升降刀功能。贝加莱开放的CNC代码可以灵活地实现连杆型面直线或抛物线型面切削,具有良好的控制性能和操作性能。
关键词:镗床;贝加莱PLC;CNC;伺服驱动器;最小二乘法
1 引言
近年来,发动机的转速、平均有效压力和活塞平均速度都较以前有了大幅度的提高,因此发动机的热负荷和机械负荷都增加了。曲柄连杆机构(如图1所示)是发动机的主要运动机构,主要由连杆小头、杆身和连杆大头组成,小头用来安装活塞销,杆身通常做成“工”或“H”型,以求在满足强度和刚度的前提下减少质量。连杆大头与曲轴的连杆轴颈相连,为了便于安装,一般做成分开式,与杆身切开的一半称为连杆盖,二者靠连杆螺栓连为一体。曲柄连杆的功用是将活塞的往复运动转变为曲轴的旋转运动,同时将作用于活塞上的力转变为曲轴对外输出的转矩,以驱动汽车车轮转动,连杆承受着巨大的压力,这些压力来自于由活塞产生的循环载荷,只有不断提高加工精度,才能满足现实高要求的标准[1]。
1-连杆小头 2-连杆大头 3-连杆杆身 4-连杆螺钉
图1曲轴连杆实物 传统镗床在加工异型销孔时不能实现程序的精确调整,并且加工过程中有一个升刀和降刀的程序调整,数控程序调整无规律可循,经常通过多次调整和检测,精度也很难达到工艺要求。本文对CNC和型面曲线进行了大量的理论和实验研究,并且在镗床上实际操作成功调试完成并得以应用。
2 镗床机械设备和工艺概述
镗床是用镗刀在工件上加工已有预制孔的机床。通常镗刀旋转为主运动,镗刀或工件的移动为进给运动。它主要用于加工高精度孔或一次定位完成多个孔的精加工,此外还可以从事与孔精加工有关的其它加工面的加工。镗削是一种用刀具扩大孔或其它圆形轮廓的内径车削工艺,其应用范围一般从半粗加工到精加工,所用刀具通常为单刃镗刀(称为镗杆),镗孔是镗削的一种。
该曲轴连杆镗床主要组成部分如图2所示,连杆镗床的机械加工过程主要是通过安装在主轴上的镗杆的相对径向摆动实现销孔型面的加工,可相互配合对所加工工件的两头同时进行对头镗孔,也可对工件单独镗孔。镗头主轴由外轴和偏心内轴两部分组成,安装刀具的镗杆安装在偏心主轴上,当主轴电机带动主轴旋转时,镗杆跟随主轴同步选装,产生一个旋转半径,刀具实现直孔加工。而当偏心内轴相对外轴有一个相对旋转时,则刀具的选装半径有一个相对主轴中心上升和下降的径向摆动,此径向摆动通过车床数控系统的控制实现各种形状的销孔异型的加工。工件安装在工作台上随工作台沿床身导轨作纵向直线移动,是通过滑台上的螺旋丝杠做往复运动实现的。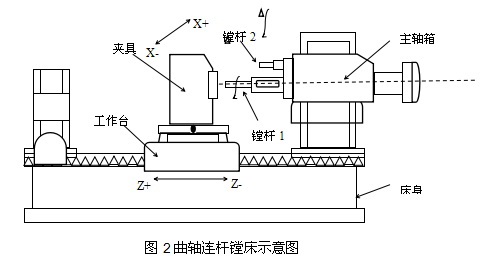 机床的控制精度,最主要的就是依靠单轴定位精度、重复定位精度和镗削精度。单轴定位精度和重复定位精度主要通过该轴行程内的定位误差范围来反映,定位精度可以通过伺服内部参数来实现,重复定位精度可以通过螺距补偿功能实现;镗削精度,是反映数控系统的插补功能,最主要依靠PLC和伺服驱动器处理器性能来满足要求,处理器性能越高,对数据密化度越高,插补曲线越圆滑,控制效果越好。
3 镗床控制系统的构成
该镗床控制系统的硬件架构如图3所示,PLC通过EthernetPowerlink接口与伺服驱动器(ACOPOSMulti)连接。EthernetPowerlink是在快速以太网基础上创建的一个高速、实时、确定的网络环境,它所支持的最快网络循环时间约为400μs,能够与伺服驱动控制周期保持同步,传输速率为100Mbps。利用高速循环数据交换,抖动必然会降到最低,同时也能在不影响循环通信情况下处理非循环数据。
图2中,连杆大头镗杆1由伺服驱动器控制交流同步电机驱动,连杆小头镗杆2由变频器控制交流异步电机驱动,工作台Z轴由伺服驱动器控制交流同步电机驱动,夹具X轴由伺服驱动器控制交流同步电机驱动,而镗杆Y轴则采用模拟量控制液压比例阀来驱动。
在应用软件中通过最小二乘法成功地给出了镗杆的位移——电压曲线,并且把这个曲线作为基本控制,得到了相当平稳而且精度相当高的的Y轴运动规律。伺服驱动器内部智能优化PID参数,成功地消除了控制信号中的扰动信号,减轻了各种干扰对系统的影响,从而大大提高了机床的可靠性。操作也更加灵活方便,调试简单,减少了控制系统的设计时间,节省了维修成本,提高了产品合格率,同时也提高了镗床的经济效益。简单灵活开放的G代码解释器设计,也为国内自主设计高精度专用数控机床提供了一种有效的方法。
图3 曲轴连杆镗床控制系统硬件架构 4基于贝加莱PLC和伺服驱动器的曲轴连杆镗床控制
4.1PLC[4]
传统PLC单纯的逻辑顺序控制功能已远远不能适应当今工业控制任务的要求,要处理一些复杂的任务,使控制系统具有较高的智能度,贝加莱PLC系统具备了大型计算机的分析能力,其操作系统是分时多任务操作系统,操作系统内核是一个具有多任务处理能力的标准操作系统,它能完成多任务间的处理与应用程序管理等最基本的功能。
分时多任务操作系统可以将整个操作界面分成数个具有不同优先权的任务等级,用户可以将任务放在不同的任务级别中。B&R的CPU模块提供了8个任务层(Cyclic#1~Cyclic#8),用户可以通过AutomationStudio集成软件平台来设置这些任务层的循环时间,循环时间可以任意设置;多任务层的执行顺序是由各任务层的优先级确定的,优先级高的任务等级总是先被执行,剩余时间里可以执行优先权低的任务等级。多任务的循环校验保证在每一个循环时间内对一个任务层的所有任务都执行一次。
一个分时多任务操作系统可以将比较重要的任务的任务等级定义的高一些,如调节任务(由用户自己定义),而一些较一般的任务可以定义的任务等级低一些,如报警任务处理任务、结果处理任务等。这样整个控制系统便得到了优化,具有较好的实时性。在曲轴连杆镗床加工系统中,把CNC和控制任务放到高优先级的任务中,实现对位置差补的精确控制,其它的如采集数据、读写数据模块、普通I/O检测、报警等任务放在优先级较低的任务中。
4.2伺服驱动器
伺服驱动器对于由应用程序或生产过程变化触发的事件的响应速度是非常重要的,控制回路扫描时间越短,就会得到更好的平滑运动特性和定位精度,贝加莱伺服驱动器的转矩、速度和位置控制其的扫描周期分别是50μs、200μs和400μs,可以实现非常完美的控制效果,伺服驱动器内部控制原理图如图4所示。
图4 伺服驱动器内部控制结构框图 其中位置环的作用是产生电机的速度指令并使电机准确定位,通过设定的目标位置与电机的实际位置相比较,利用其偏差通过位置调节器来产生电机的速度指令。当电机开始起动后(大偏差区域),应产生最大速度指令,使电机加速并以最大速度运行;在小偏差区域,产生逐次递减的速度指令,使电机减速运行直至最终定位,它保证系统静态精度和动态跟踪的性能,直接关系到交流伺服系统的稳定与高速运行。
转矩环可以改变内环控制对象的传递函数,提高系统的快速性,及时抑制环内部的干扰,限制最大电流,使系统有足够大的加速转矩,并且保障系统安全运行。
速度环的作用是保证电机的转速与设定值一致、消除负载转矩扰动等因素对电机转速的影响,速度指令与反馈的电机实际转速相比较,其差值通过速度控制器产生电流参考信号,该信号控制电机加速、减速或匀速运行,从而使电机的实际转速与设定值保持一致。
5 拟合镗杆位置电压曲线
最小二乘法(又称最小平方法)是一种数学优化算法。它通过最小化误差的平方和寻找数据的最佳函数匹配。利用最小二乘法可以简便地求得未知的数据,并使得这些求得的数据与实际数据之间误差的平方和为最小[2]。
最小二乘法可以用来处理一组数据,可以从一组测定的数据中寻求变量之间的依赖关系,测得变量之间的n个数据,则在平面上可以得到n个点,这种图形称为“散点图”,从而可以粗略看出这些点大致散落在某直线近旁,我们认为点与点之间近似为一线性函数,最小二乘法在该设备中用于拟合镗杆Spindle轴的输入电压和档杆纵向位移曲线。
图5 镗杆升刀示意图 主轴进给方向即为Z正向,与主轴轴向垂直的方向为Y正方向,如图5所示,Spindle轴变频调速,控制简单,只需恒定转动即可;镗刀由0~10VDC模拟量控制液压比例阀,通过调节电压达到镗孔的半径大小。以升刀为例,通过给定1V、2V、3V、4V…10V信号,分别检测得到Y轴的位移(单位0.001mm),如图6所示。得到采样点之后,选择中间线性度较好的几个点,由最小二乘法线性化处理,可以拟合得到一条直线,表达式为y=k·x+b,如图7所示。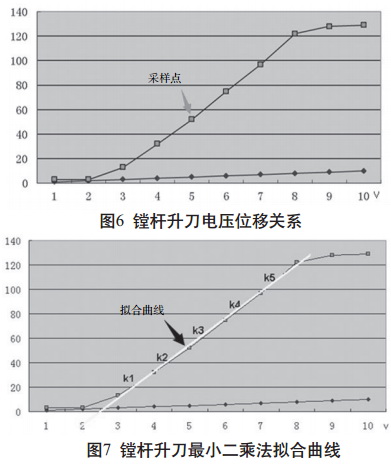 6G代码解释器
数控机床是依靠加工程序对工件进行加工的自动化设备,加工程序记录了数控加工的一切必要信息:零件加工的工艺顺序、运动轨迹与方位、工艺参数(转速,进给量和切削速度)以及辅助功能(换刀、变速、切削液的开启)。在CNC系统中,无论是自动生成还是手工编制的数控程序,计算机都无法直接根据数控程序进行加工,必须通过解释程序提取数据,转换为计算机可以执行的程序,以供计算机进行加工仿真或控制机床加工实际零件。因此数控代码解释器也就成为CNC系统的一个重要模块[3]。
由于该设备所涉及的G代码的专用性与特殊性,国际标准化组织(ISO)规定的标准编程指令全部不适用于该系统,所以需要设计专用的G代码,贝加莱采用XML语言编写解释器。XML能方便有效地表示结构化数据,这就使得XML可以作为描述和传输数据的手段,使用XML进行数据交换已经成为计算机软件领域的标准技术模式。机床辅助功能上的指令需要人为定义M代码。
抛物线型面表达式为:y=A·Z2+B·z+C
y—镗杆纵向位移
z—平台水平位移
图8 曲轴连杆型面抛物线切削面路径示意图 调用G代码格式:G995/G996Z<绝对位置值>A<系数值>B<系数值>C<系数值>
7总结
该镗床实际用来为戴姆勒重卡加工配套曲轴连杆,通过活塞型线测量仪分析型面镗削精度,上下限范围在±2um,如图9所示,实际加工曲线在虚线范围内,满足要求,达到设计精度。
图9 型面切削路径分析曲线 数控系统开放化已经成为数控系统的未来之路,所谓开放式数控系统就是数控系统的开发可以在统一的运行平台上,面向机床厂家和最终用户,通过改变、增加或剪裁结构对象(数控功能),形成系列化,并可方便地将用户的特殊应用和技术诀窍集成到控制系统中,快速实现不同品种、不同档次的开放式数控系统,形成具有鲜明个性的名牌产品。贝加莱数控系统正是开放性系统的典型代表,而且在多个行业展示其较高的效能。
参考文献
[1]陈云卿,杨顺田.数控铣镗床编程与技能训练.化学工业出版社,2008,10.
[2]陈宝林.最优化理论与算法.清华大学出版社,2003,9.
[3]赵东林,方凯.数控系统G代码解释器的设计与实现.制造业自动化,2006,1.
[4]齐蓉,肖维荣.可编程控制器技术.电子工业出版社,2009.(end)
|
|
文章内容仅供参考
(投稿)
(如果您是本文作者,请点击此处)
(3/28/2011) |
对 镗床/钻床 有何见解?请到 镗床/钻床论坛 畅所欲言吧!
|