阀门 |
|
| 按行业筛选 |
|
|
| 按产品筛选 |
|
|
| |
查看本类全部文章 |
| |
|
|
|
电液伺服阀先进工艺检测技术 |
|
作者:哈尔滨工业大学 王广林 |
|
我国航空、航天及军工等部门的精密机械零件的机械加工生产的主要特点是:高精度、复杂形状和难加工材料的零件多,新型号多、品种多、批量少,很多零件属于试制性生产。很多关键性零件由于精度很高、配合上有特殊要求等,对于配合零件在工艺上多采用“偶件配做”或“试验筛选”的方式制造。这种生产方式需要一种特殊的检测方式伴随着零件的加工制造过程。
本文以电液伺服机构中的关键部件电液伺服阀的零件为例阐述先进工艺检测技术及其应用。电液伺服机构广泛应用于航空、航天等需要功率大、快速、精确反应的控制场合,有制造难度大、成本高的缺点。这些缺点尤其突出出现在电液伺服阀的各零件的加工制造过程中。在电液伺服阀阀芯和阀套(见图1)的制造中,目前我国所有军品生产厂家均未做到互换性加工。不论是径向尺寸直径D ,还是轴向尺寸A 、B 、C (和A 1 、B 1 、C 1)都是采用偶件配磨的方式加工,阀芯阀套一一对应,没有互换性。以加工轴向尺寸的配做为例,一般是先加工好阀套方孔工作边的尺寸A 、B 、C ;然后将阀芯装在阀套内一起测量轴向配合尺寸情况;再根据测量结果磨削阀芯端面,从而保证阀芯工作边与阀套工作边轴向尺寸的配合要求。
图1 电液伺服阀滑阀副示意图 从上述举例可以看出,此种加工与传统的互换性调整法机械加工不同,它是采用加工-测量-再加工-再测量的反复多次的工艺过程,最终达到技术要求的。伺服阀的加工要求特殊,因此在生产中需要很多专门的工艺方法和专用的仪器检测方法和设备。
先进工艺检测技术的概念
传统批生产互换性制造工艺中,检测工序一般是中间检验和最终检验。其目的大多是控制废品率和作为调整机床和维护工艺装备的依据。其形式一般采用专用工序或直接送计量室、检定站等专业部门检测。
区别于上述检测工序,在航空航天等精密制造领域特有的检测技术,是与加工制造工艺为一体的,是精密零件制造中为达到某一关键技术要求所采用的整个工艺方法中的一部分。因此,我们将这种随制造工艺过程而进行的、现场的、在位的,甚至是在线的检测称之为“工艺检测”。
根据上述定义,不难看出“工艺检测”技术有以下特点:
(1)不是验证性检验,亦即不是给出“合格”与“不合格”的信息,而是要给出进一步加工的数值和方向,因此是属于“边干边看”制造方式中不可缺少的“看”的过程,对工艺方法影响极大;
(2)是在加工现场的检测、计量,一般不是由专门的检验人员操作完成,往往直接由加工者检测,是一种现场的、在位的或在线的实时检测;
(3)检测设备和方法往往是专用的,一般必须结合具体工艺需要试验、设计、研制专门测量方法和仪器设备;
(4)精度和效率都有较高要求。
上述的“工艺检测”技术的特点决定了其专用性强,使用面窄,故国内也始终没有专业生产厂家生产制造有关工艺检测的设备仪器。因此,国内军工生产部门在生产过程中还部分采用一些较为落后的工艺方法和仪器检测设备,甚至在某些关键零件的加工中还采取了较为原始、落后的所谓“土办法”来适应生产需要。这种测量方法操作繁琐,工作量大,还需计算,读数误差大,效率低,制约了精密零件制造工艺的发展。
为了提高航空航天等行业精密零件工艺检测的水平,我们提出了先进工艺检测技术的概念。先进工艺检测技术是将现代计算机、微电子技术和传感器技术应用于工艺检测中,结合精密零件制造的工艺特点,采用先进的工艺检测方法,实现精密零件的高精度、自动化检测。先进工艺检测技术包括两个方面的内容。
(1)采用当代先进的计算机数据采集和控制测量过程技术,利用传感器等先进手段,进行自动化测量、数据采集处理和结果打印、输出记录存档等。
(2)采用区别于传统工艺检测方法的先进工艺检测原理,利用相对法测量、非接触式测量等先进测量技术,使工艺检测更具科学性、合理性。
以下结合我们的科研成果,介绍一些先进工艺检测技术的方法和应用。
自动化流体式测量技术
自动化流体式测量技术是一种利用现代计算机技术和传感器技术,以测量流体的流量或压力来间接测量微小几何量的一种工艺检测技术。这种检测方法不仅仅是单纯的流体特性测量,流体特性测量是为工艺检测服务的。流体式工艺检测所利用的测量介质可以根据需要选用气体或者液体,相应的可区分为气动测量和液动测量两种类型。这里主要以电液伺服阀的滑阀副叠合量配磨测量为例,介绍自动化流体式测量的基本原理和方法。
伺服阀的叠合量是伺服阀、滑阀加工过程中需要严格保证精度的关键的设计和工艺参数,它是指滑芯在阀套中位时,阀芯台肩的工作棱边和阀套相应方孔的工作边的轴向配合尺寸。对于最常用的四开口滑阀(见图2),由于有4个阀口,因此相应有4个叠合量需要保证,即图2中的L a~L d。伺服阀叠合量的实质是滑阀中位时各个节流口的开口形式。
图2 滑阀叠合量示意图 由于叠合量对伺服阀的性能有很大影响,因此在设计上对伺服阀滑阀叠合量的要求非常严格,一般配合精度为1~2μm的范围[2-3]。叠合量的加工都是采用偶件配作的方式进行,由于一般采取磨削阀芯台肩去配已提前加工好的阀套的方法,所以叠合量的加工称为“配磨”[3]。开始配磨时滑阀各节流口叠合量通常留有几百微米的加工余量,到最后加工完毕要经过“测量-磨削-测量”几次反复的过程,叠合量加工的精度需要用测量来保证。
从原理上讲,可以按叠合量的定义分别计量阀套方孔4个平面之间的相对位置尺寸和阀芯4个台肩端面之间的相对位置尺寸,即可计算出叠合量的数值。但事实上并没有采取这种测量的方法,这种方法也不可能准确地测量出滑阀的真实叠合量。主要原因:叠合量实际上是棱边之间的距离,而测量点只能是落在形成工作棱边的端面上,不可能落在阀口工作棱边上,这就造成了测量的不准确性。而且阀口棱边处有可能存在有塌边、圆角以及必然存在的径向间隙等诸多非理想情况,所以间接测量的方法不能反映阀口的实际情况。真正实用的办法是利用某种装置使各阀口通过某种流体介质,利用介质的流量或压力等参量的变化来间接反映各阀口之间在轴向的相对位置关系(即叠合量),可以称之为叠合量的流体式测量法。
早期气动测量方法较为原始,采用手动的气动综合测量法[4-5]。这种测量方法最初尚能应付试制性军品生产方式下的单件小批生产规模,但当批量稍大,精度要求更高时就难以满足生产要求了。
1 基于压力式气动测量的叠合量测量
如图3所示将伺服阀的环形节流口展开后可以看成是一种喷嘴盖板机构。经稳压后的压缩空气P g流经面积梯度为w 开口量为x 的方孔,再流经节流喷嘴d 溢入大气。改变开口量x 可以改变P c的大小,故可通过测量P c来度量x 的大小。
图3 单阀口气动测量气路图 由气动测量的理论可知,当节流喷嘴直径d 和气源压力P g都选定时,P c与x 的关系如图4所示。
图4 P c与x 的关系曲线 由于P c与方孔开口量x 是非线性的关系(见图4)。为了能方便地找出零开口位置,必须将特征方程线性化。通过测量不同开口大小的P c值,并进行线性化处理就可以得到xv -Y 的测量曲线,从而获得阀口的零开口位置,并以此计算出伺服阀的叠合量L a~L d。
采用公式变换法来线性化特征方程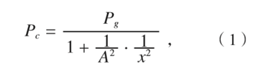 将特征方程改写为 ,并令 则,Y =A x 。
在实际测量过程中,由于上式为线性方程,所以对于各个节流口只需测出一组(P ci,x i)值,再利用式(2)算出Y i。对测量点采用最小二乘法进行线性回归计算,就可得到线性回归方程Y =A x +B 。
对入滑阀副的4个节流口可以得到如图5所示的4个零开口位置x a0,x b0,x c0,x d0后。选定一个基准点坐标x 0=(x b0+x c0)/2,再分别计算出各边的叠合量数值。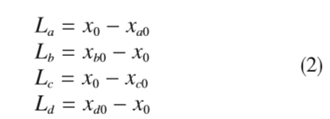
图5 压力式气动测量特性曲线 采用计算机测控技术、传感器技术,并基于以上原理设计并开发了叠合量气动自动测量系统,替代了传统的手动测量土办法。
2 基于流量式液动测量的叠合量测量
气动测量法具有分辨率高、适应能力强、易于实现多参数综合测量等优点。但是气动测量法采用的介质与伺服阀实际使用的介质航空液压油不一致,且气体无粘性,对泄漏敏感。经分析,对于额定流量大的伺服阀更益采用液动法进行测量[6-7]。
流量式液动测量原理如图6所示,压力为Pg的液压油通过伺服阀滑阀的矩形节流口,并流经流量计后回到油箱。阀口的开口量xv可以通过测量通过阀口流量的大小来间接测量。
图6 流动式液动测量原理图 阀口的流动状态可以用薄壁孔口淹没出流的流量计算公式来描述。流量的计算公式为: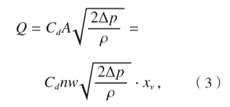 式中,Q 为通过阀口的体积流量;△p为阀口前后压力差; ρ为液压油密度;A 为阀口的过流面积,对于理想滑阀阀口A =nwxv;C d为流量系数,在一定条件下为常数。
当阀口压差△p恒定,液压油可以看作不可压缩流体,因此密度ρ也为常数。根据式(3),各个阀口的流量可写为Q =Kxv +B 。类似气动法叠合量测量的处理方法,可以得到滑阀副的叠合量值[8]。
3 气动窄缝扫描测量
阀芯和阀口所形成的阀口节流工作棱边是电液伺服阀的关键结构,其加工质量直接影响电液伺服阀的整体性能。棱边端跳动为阀口节流工作棱边的加工质量的重要指标。然而,由于节流工作棱边处于阀套内侧、精度要求高、易于损坏等原因,棱边端跳动无法利用通用测量设备进行检测。
测头做成窄缝状,当其沿着被测棱边运动时,就能够将被测棱边的端跳动测量出来。如图7所示,这种方法可称为“气动窄缝扫描测量法”。
图7 气动窄缝扫描测量法基本原理 如图8所示,根据不同测量对象的具体形状和测量要求来设计专用的气动窄缝扫描测量法测头。用于测量阀套方孔工作棱边跳动,测头可设计成图8所示的芯型。
图8 利用气动窄缝扫描法进行阀套和阀芯工作棱边跳动测量 保持测头与阀芯轴向位置关系不变,旋转阀芯或测头时,阀芯棱边轴向几何误差必然反映到开度S 的变化上,从而引起pc值的变化。通过压力传感器把压力转化为长度尺寸量、可以将几何形状精度(轴向跳动量)测量出来。
4 伺服阀小孔配对测量
双喷嘴挡板力反馈两级电液伺服阀是电液伺服阀的主要类型,是目前应用广泛的电液伺服阀之一。
喷嘴是双喷嘴挡板阀的重要零件,双喷嘴挡板阀为对称式结构,即在一个喷嘴挡板阀中有两个喷嘴,对于它们前端的节流小孔有严格的对称性要求,一方面体现在结构上的对称性,另一方面体现在流体性能上的对称性要求。双喷嘴挡板阀的结构对称性可在伺服阀在液压零位调整时通过调整喷挡间隙来保证。而对流体性能对称性,需要通过对一批喷嘴进行压差流量测量,然后再根据测量数据进行配对,筛选出对称性好的两个喷嘴(即两者的压差流量值之差小于配对要求)来保证。我们研究了一种伺服阀喷嘴自动流量配对测量技术,并研制了一系列计算机控制的喷嘴压差流量自动测量系统,实现了喷嘴流量的自动测量和配对[9-14]。
配对测量包括了压差—流量和压力测量两个部分。其中压差—流量特性的测量原理如图9所示。采用压力传感器1和2分别测出喷嘴前端的压力值和出口处的压力值,用齿轮式流量计测量此压差下通过喷嘴的流量值,进行一系列的调压和测试后得出喷嘴的一系列压差值和对应的流量值。
图9 压差—流量特性的测量原理 压力特性测量原理如图10所示,在喷嘴前面串联一个标准节流孔,控制前后压力差在要求范围内,即△P=P1-P2 ,采集中间传感器P 0对应的压力值。根据液流连续定律,通过标准节流孔和被测喷嘴的流量相同,若被测孔的节流特性高于标准节流孔则P 0值会升高,反之则会下降。记录下每个喷嘴的压力值P 0,然后选择压力值之差在配对范围之内的两个喷嘴配对使用。
图10 压力特性测量原理 编制测试系统软件,通过调用数据库存储的测量数据,并根据算法实现了伺服阀小孔零件的自动配对。
智能化电动式测量技术
用电量(电压或电流等电参数)的变化来测量几何量(如尺寸、形状和位置)或物理量等非电量的方法称为电动式测量。电动式测量的工作原理是将被测参量(如微小位移)变化,转换为电信号,再经放大或运算等处理后,用指示表指示,用记录器记录,或去控制一定的执行机构。
先进工艺检测技术中,电动式测量方法应用很广泛,本文仅介绍具有代表性的伺服阀中的关键弹性元件弹簧管的刚度值的测量方法。
为了改变测量精密弹性元件的落后状况,我们研究了刚度测量技术。采用传感器、微处理器等先进技术实现了刚度测量的全自动化测量,现已得到广泛应用。适用范围也由测量伺服阀中反馈杆弹簧管等发展到测量更高精度的陀螺仪中的挠性接头、扭杆、摆杆等。
如图11所示,将弹簧管装在夹具中夹紧,并在弹簧管头上装测量杆,通过旋动手轮推动施力头向上平行运动,与测杆接触后产生向上的推力F 1,在此推力作用下弹簧管产生变形,测杆头部上升△S=S1-S0。分别通过力传感器测出F 0和F 1,位移传感器测出S 0和S 1,则刚度值为: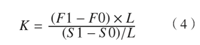
图11 弹簧管刚度测量的变形示意图 光学CCD显微检测技术
航天精密零件加工中有些场合需要非接触式高精度的多参数综合测量,如阀口工作边微观形貌,喷嘴环带几何形状误差在位测量等。为此,我们研究了光学CCD显微检测技术。
在伺服阀的生产中往往采用工具显微镜观察棱边的加工质量,但都是定性地看看是否有较大的微观毛刺和较大的塌边、蹦口等,不能定量地测量具体加工质量指标,因此只能作为一种质量监视的参考手段用于生产。分析光学显微镜观察不能进行定量测量的原因,主要是难以准确读数和记录,若采用投影仪或读数显微镜等仪器测量,则测量效率低,人为读数误差较大,难以实现自动读数、记录和数据处理,生产中也很少采用。
为了测量阀口棱边加工质量,我们研制了一套CCD光学显微检测系统,其测量原理如图12所示,将CCD摄像头对准倾斜45°的阀芯棱边,使棱边成像于面阵CCD棱边上,经图象采集卡采集到计算机中,并显示于显示器屏幕上,棱边图像可放大500倍以上,其微观几何形貌清晰可见,经过计算机图像处理后,可以得到微观形貌的测量值(棱边粗糙度R a)。若将棱边的阀芯水平放置,镜头沿切线方向对准阀芯,则可以观测棱边圆角和毛刺参数。
图12 CCD显微测量阀口微观形貌原理 加工检测一体化技术
直接由设备自动完成“边加工边检测”的全自动加工过程,才是真正意义上的“加工检测一体化技术”[15]。我们研究了基于微驱动及在线测量技术的阀芯工作边精密磨削技术,并开发了“闭环控制滑阀轴向配磨系统”。现介绍一下加工检测一体化技术的基本思想和实现方法。
对于伺服阀滑阀偶件的轴向配合尺寸——叠合量的保证,由于其精度要求太高,国内生产中几乎均不采用互换式加工,而全部采用偶件配做的形式生产,也就是所谓的“配磨”。配磨的过程是:加工-测量-加工-再测量,往往是需要几个反复的过程,到最后阶段,经常遇到去除1~2μm余量的情况。这时全凭工人的经验和操作技巧来完成磨削任务。磨削量很难严格控制,稍有不慎,就会出现废品。
针对上述情况,我们研制自动控制的微进给系统(见图13),同时安装测头直接测量工件被磨削表面,做到边磨削边监测,一旦达到预先设置的磨削量,立即停止进给,退回工件,完成加工。这样一种思想即为闭环轴向磨削控制的原理。
图13 阀芯磨削微进给系统原理图 系统的工作原理是:微进给顶尖在驱动电源输出的直流电压的驱动下推动工件右移,电感测头直接测量被磨削工件的加工面,并且通过调整机构安装在后顶尖上,与工件一起运动,当工件加工表面被砂轮磨去时,测头摆动将磨削量变化的电信号反馈给驱动控制器内的单片机,单片机判断是否到加工终点,如果没到,则继续控制顶尖伸长,直到加工结束。由于微进给装置是可控的,所以整个磨削进给过程也是受控的,根据需要可以采用各种不同的进给方式和加工速度曲线,如“先快后慢”或“匀速进给”等。
传感器采用侧摆式位移传感器,测头安装在滑动尾座上,可以在阀芯轴向和径向方向上进行调整,并且有绕阀芯轴向旋转的自由度,方便拆卸阀芯。
结束语
先进工艺检测技术是一种伴随精密零件制造工艺过程的、采用现代计算机和传感器技术的新型检测技术。本文介绍了自动化流体式测量技术、智能化电动式测量技术、光学CCD显微检测技术和加工检测一体化技术等采用先进工艺检测技术的方法,对先进工艺检测技术的应用进行论述。应该指出,先进工艺检测技术目前在已有研究的基础上,还处于进一步发展阶段,而研究在位的,甚至是在线的加工检测一体化技术,开发高效率、智能化的新型检测设备,是先进工艺检测技术进一步发展的方向。(end)
|
|
文章内容仅供参考
(投稿)
(如果您是本文作者,请点击此处)
(5/21/2015) |
对 阀门 有何见解?请到 阀门论坛 畅所欲言吧!
|